
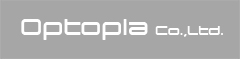
JP / EN
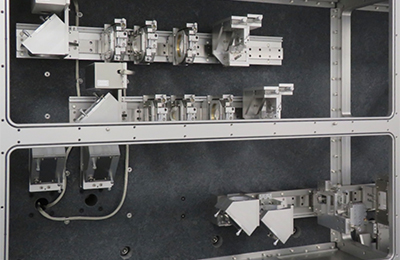
Solution
Laser Lift Off system
In the manufacture of flexible displays, devices are manufactured by the laser lift-off process.
In the process of laser lift-off (LLO) and UV laser peeling (ULP), the process using the line beam laser optical system is active.
What is laser lift-off ?
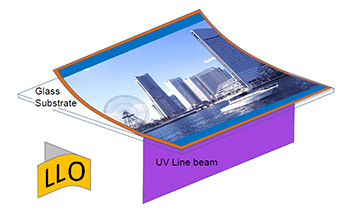
Flexible OLED displays are manufactured using the Laser-Lift-Off (LLO) process. Laser lift-off is a processing method that peels off only the device layer by irradiating a laser from the back side of the device laminated on glass or a transparent substrate to ablate the interface between the glass and the device.
If it can be ablated using a substrate that transmits laser such as transparent glass, it can be easily peeled off due to the stress generated at the interface.
In the conventional lift-off of GaN devices in LED manufacturing, the irradiation of a uniform beam with a relatively small die area and a small area was sufficient, but in flat panel display applications, it is necessary to lift off the entire area of a large substrate. The process is activated.
If it can be ablated using a substrate that transmits laser such as transparent glass, it can be easily peeled off due to the stress generated at the interface.
In the conventional lift-off of GaN devices in LED manufacturing, the irradiation of a uniform beam with a relatively small die area and a small area was sufficient, but in flat panel display applications, it is necessary to lift off the entire area of a large substrate. The process is activated.
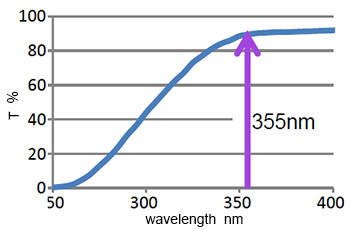
The graph on the left is the ultraviolet transmittance curve of alkali-free glass.
It can be seen that 355 nm laser light, which is the wavelength of a general UV solid-state laser, transmits approximately 90% of glass.
Depending on the type, the 3rd harmonic UV solid-state laser has lasers of 351 nm and 343 nm in addition to the oscillation wavelength of 355 nm.It can be seen from this graph that any wavelength has sufficient transmittance for glass. This means that any third harmonic UV solid state laser can be used.
Depending on the type, the 3rd harmonic UV solid-state laser has lasers of 351 nm and 343 nm in addition to the oscillation wavelength of 355 nm.It can be seen from this graph that any wavelength has sufficient transmittance for glass. This means that any third harmonic UV solid state laser can be used.
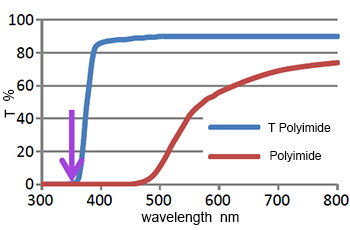
The graph on the left is the transmittance curve of polyimide and transparent polyimide.
It can be seen that the 355 nm laser light, which is the wavelength of a general UV solid-state laser, has a transmittance of about 0%, that is, an absorptance of about 100%. Also, as mentioned above, this graph shows that any third harmonic UV solid state laser has an absorption rate of about 100% for polyimide.
Therefore, any third harmonic UV solid state laser can be used.
It can be seen that the 355 nm laser light, which is the wavelength of a general UV solid-state laser, has a transmittance of about 0%, that is, an absorptance of about 100%. Also, as mentioned above, this graph shows that any third harmonic UV solid state laser has an absorption rate of about 100% for polyimide.
Therefore, any third harmonic UV solid state laser can be used.
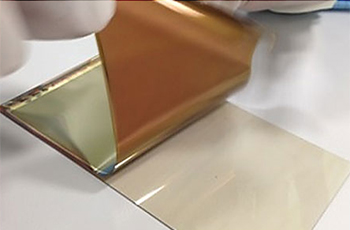
Based on this, by stacking a polyimide thin film on a non-alkali glass substrate and manufacturing a device on it, a laser lift-off process is performed using a third harmonic UV solid-state laser with a wavelength of 355 nm or 343 nm. This allows laser ablation of the polyimide layer and easy peeling of the device layer. This process produces a flexible display device. These are used for foldable smartphones.
Laser lift-off system
VOLCANO® Line Beam systems can be designed with different line lengths up to 750mm and 1000mm. The use of solid state lasers emitting UV light at 343nm reduces the operating costs and increases the uptime of production tools remarkably, compared to systems using excimer lasers.
The LB systems are based on a rigid aluminum housing structure and the FALCON XXL projection lens gives a working distance of >200mm. A stable and solid system structure is needed to support the line beam optics. Line Beam Optics include a MBC (Manual Beam Control) camera system which allows to control and adjust position and angle of all laser emitted beams. The FALCON XXL design contains a window which seals the optics from the process chamber and protects against contaminations from the process.
The energy density of >500mJ/cm2 is obtained by using 6 TruMicro 8320 (20mJ specification) with 750mm x 20µm FWHM line beam. The Line Beam optics give a DoF ≥300µm for a 20µm FWHM small axis and a uniformity of p2p ≤10%.
The LB systems are based on a rigid aluminum housing structure and the FALCON XXL projection lens gives a working distance of >200mm. A stable and solid system structure is needed to support the line beam optics. Line Beam Optics include a MBC (Manual Beam Control) camera system which allows to control and adjust position and angle of all laser emitted beams. The FALCON XXL design contains a window which seals the optics from the process chamber and protects against contaminations from the process.
The energy density of >500mJ/cm2 is obtained by using 6 TruMicro 8320 (20mJ specification) with 750mm x 20µm FWHM line beam. The Line Beam optics give a DoF ≥300µm for a 20µm FWHM small axis and a uniformity of p2p ≤10%.
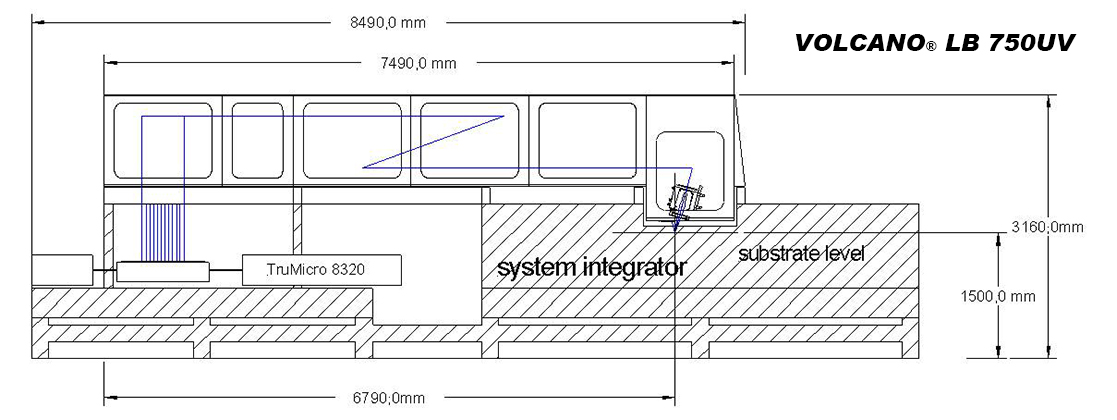
VOLCANO® Line beam laser system specifications | |||
Model name | VOLCANO® 100UV | VOLCANO® 300UV | VOLCANO® LB 750UV |
Wavelength | 343nm | ||
Beam length | 100mm (Top hat) | 300mm (Top hat) | 750mm (Top hat) |
Beam width | 20 - 30μm FWHM(Gaussian) | ||
Energy density | 630mJ/cm2@20μm FWHM | 310mJ/cm2@30μm FWHM | 370mJ/cm2@30μm FWHM |
Beam uniformity | p2p < 6% best focus | ||
Laser | TruMicro 8320 | TruMicro 8320 or TruMicro 8340 | TruMicro 8320 or TruMicro 8340 |
Pulse width | 15-20ns FWHM |